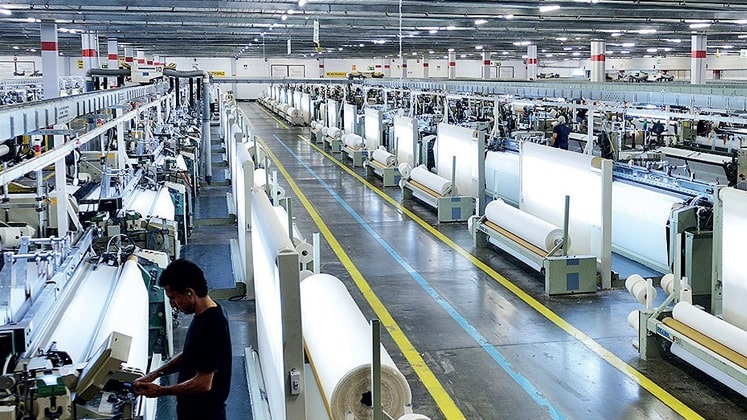
With a long history of textile manufacturing dating back to the Ottoman Empire, Turkey remains an important country in the global textile and apparel industry. The country ranked as the sixth largest exporter of textiles worldwide, accounting for almost five percent of all exports.
Turkish textile and clothing industry has a significant role in world trade with the capability to meet high standards and can compete in international markets in terms of high quality and a broad range of products. A large proportion of the textile and apparel goods leaving Turkey to arrive in locations inside the USA and Europe, with Germany, the United Kingdom, Spain, and Italy ranking as the top four destinations.
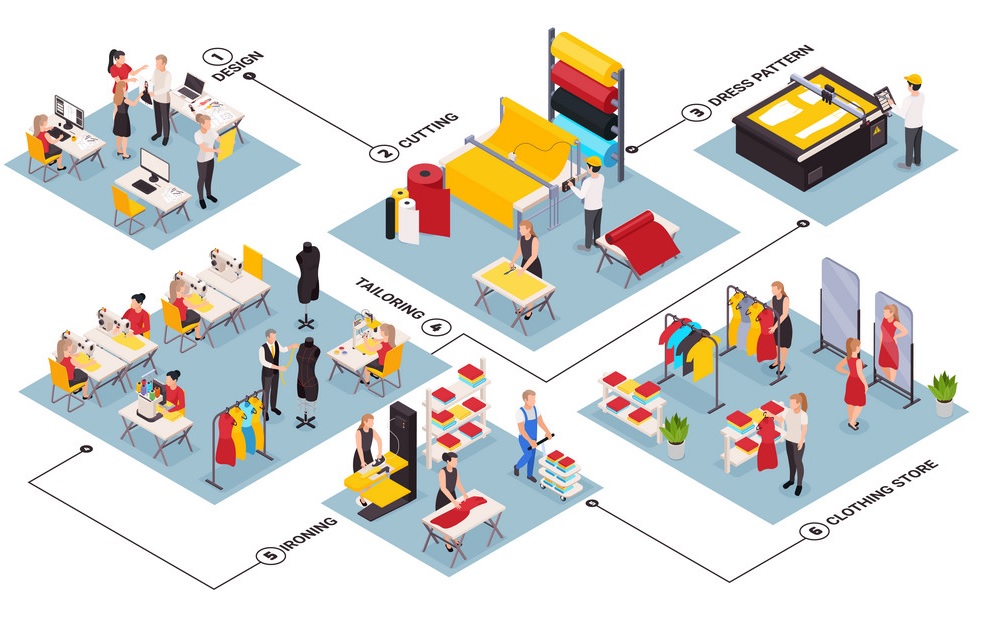
Whether consumer or retailer receives your textile product, you need to make sure that they are as they should be. Our textile inspections are customized by combining our standard garments inspection checklists with your unique product specifications. We verify the quality of mass production based on your Acceptable Quality Limits (AQL), identifying and classifying defects to offer an overview of your product’s quality.
We also perform on-site tests and assess compliance with your product’s specification and approval sample. Checks include sizing, measurements, labeling, packaging, and packing. Such as;
COLOR: Do the colors match the colors requested in the order? Do they match the sample? Is the color consistent in all products; i.e. there is no shading?
MATERIALS: Is the quality of the materials identical to the sample? Is the quality consistent across all pieces?
ODORS: Does your garment smell of textile ink, mold, or cigarette smoke?
SIZE AND DIMENSIONS: Are the products the same size as the original sample or order request? Are the dimensions accurately duplicated in production?
WEIGHT: Is the weight of the finished product the same as the original sample?
FINISHES: Have the requested finishes been added, such as linings, closures, hooks, etc.? Are they exactly like the sample?
NOTIONS: Are the buttons, zippers, snaps, etc secure and strong?
CONSTRUCTION: Are the products durable? Do the seams pull? Is the metal pliable?
STITCHING: Is the stitching strong and the same as the sample?
PACKING: Is the quality of the label, tags, and polybag as you requested?
Make sure to double-check any rush orders you have placed to confirm that the rush didn’t compromise the Quality.
Inspection Time:
1- Pre-Production Inspection: Inspection includes which kind of raw materials will be used and checks for the understanding of the buyers’ requirements from the supplier side.
2- During Production Inspection (DUPRO ): It takes place 20 to 50 % of total production has come out of the lines. Allows the buyer to have an idea of average product quality, early in the production cycle.
3- Pre-Shipment Inspection (Final): It takes place once 80-100% of the shipment quantity is finished and at least 80% is packed. It is the most common type of Quality Inspection check.
Inspection Method: We can make inspections in two different methods;
a) By sampling: We select from the whole quantity of your order a sampling lot, quality of selection lots represents the overall quality of your whole order according to the international AQL quality control method MIL-STD-105E / ISO 2859-1.
b) Full Inspection: Means the control of each and every piece of your order before shipment. It is mostly performed at the end of the production.
We have additional Services:
Container Loading Supervision: Supervising and picturized reporting the loading of products into shipping containers.
Sample Picking: Sending samples to the buyer or accredited partner labs, preparing picturized reports.
Factory Audits: Audition to your potential Turkish supplier before you start doing business with them and picturized reporting.
Sourcing Agent: Fulfill your business’s procurement requirements; comparing different suppliers, logistics, quality, intellectual property risks, etc.
During a Quality Inspection, we check for;

- The quantity produced (semi-finished, finished and packed)
- The product specifications (sizes, colors, materials)
- The visual appearance and workmanship (cosmetic check)
- All possible functions tests and safety tests
- The labeling and marking
- The packing and packaging
- Other checking points requested by clients

What are the steps to have a service?
- E-mail Contact
- Booking
- Set Inspection Date
- Payment
- Inspect & Report
- E-mail us your inquiry at [email protected]
- Fill out the booking form and email it back to us.
- We contact the supplier to schedule the final inspection date. Then the invoice will be issued to you.
- Clients arrange the service payment at least one day before the inspection date.
- Our inspectors/auditors conduct the work and provide a detailed report to the client within 24 hours after inspection.
For regular customers with monthly inspections, we also propose great discount prepaid packages of 5, 10 or 20 inspections