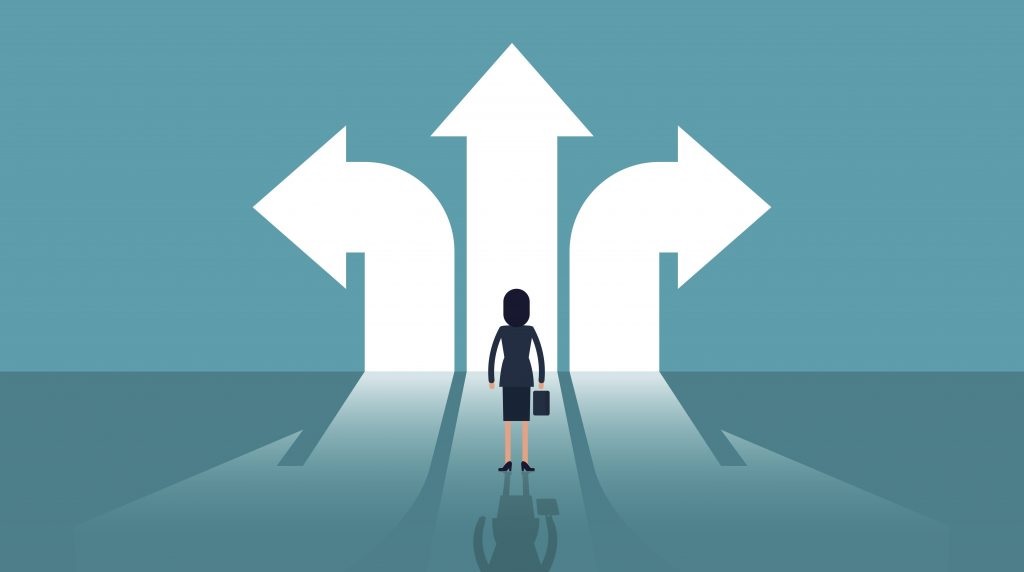
Importers often play a delicate balancing act between reducing quality control expenses on the one hand and minimizing product liability risks on the other. Many small importers are cornered in a situation where they have to sacrifice quality control. The results? Higher risks for the importer. The question is, how to solve this dilemma?
Importers are supposed to be aware of what they cannot sell on their domestic market, so they should be punished heavily whenever they resell unsafe products in their country.
Here are the comments from a Chief Quality Control Inspector:
“I would add that it is important to understand the supply chain itself, and who should hold the highest liability when unsafe imports are put on western markets.
My point is that it is easy to blame it on the Importer – often an SME – when he is only recruiting the cost pressure he gets from the final distributor (big retail groups) on his own suppliers. Ultimately, the real decision-makers on the quality of imported goods are often big corporate retailers, who won’t deal directly with factories, and who transfer the liability and risk of importing to smaller specialists importers.”
In other words, mega-retailers tend to buy more and more from intermediaries, who in turn take full responsibility for managing production. In this case, importers are pressured into accepting razor-thin margins. And of course, the fees corresponding to quality control (inspections and lab tests) would reduce this margin to an intolerable level.
Importers that don’t make sure their products comply with their country’s laws are guilty, but not entirely responsible. In a sense, they are forced into illegality–or at least into taking huge risks–just to stay in business.
To exemplify; for a European importer who was buying products of fabrics and lighting system. Local laboratories offer the tests needed to confirm this product’s respect of EU regulations. The bill from a local SGS lab: nearly USD6,000. Mostly it is higher than the amount of margin the importer plans to make! In the end, the buyer asks for certifications from his vendor. Of course, the supplier will produce such a document: he does not bear serious legal risks, and he does not want the order to be canceled. On his side, the importer knows perfectly that the certification he receives means nothing–the supplier would never pay these USD6,000 on his own to check what his own supplier sells to him.
— Responsibility should be diffused. If there are big retailers in the supply chain, forcing them to retain some liability and not transferring it all to the importer in their contracts. But how to change the system?
— Increased regulation (higher penalties and controls by customs) might have an impact, however only to a point. The cancellation also a big problem for an importer as well, not the only exporter.
— Test Laboratories should cut prices by removing some bells and whistles in their service offer.
— ***Double check; let the vendor get certifications and at the same time contact with a third-party inspector to apply Quality Control (Pre-Production and Pre-Shipment) for the products. Prepare a comprehensive checking list and tests that are possible on site and contact an inspection with the help of Quality Inspectors.